RENDERING SYSTEM
Low Energy Dry Rendering
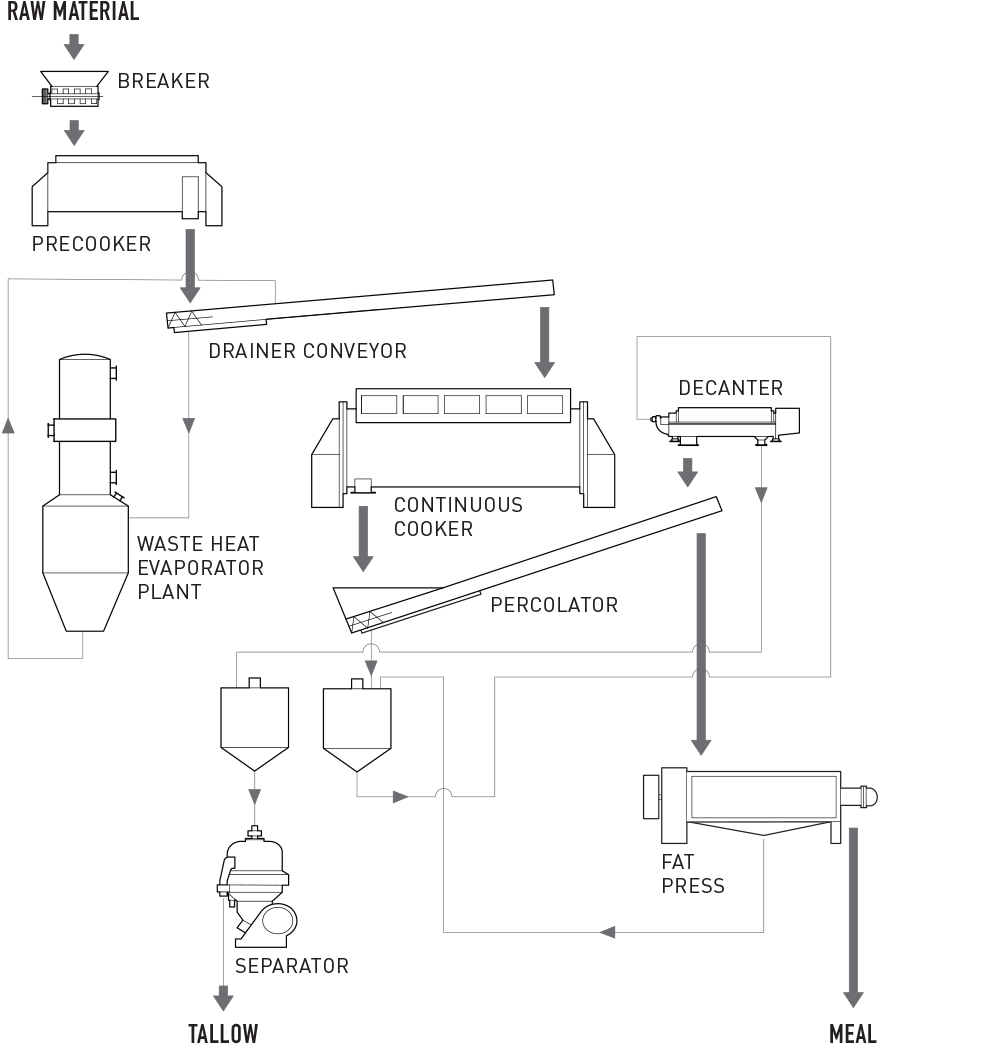
The Rendertech Low Energy Dry Rendering (LEDR) process is a modified continuous dry rendering process designed for reduced energy use. The LEDR process preheats the raw material in a Precooker, removing some liquid for concentration in a Waste Heat Evaporator. By using waste heat from the Cooker as an energy source in the Waste Heat Evaporator, overall energy use is less than in the continuous dry rendering process. The LEDR process can be retrofitted to existing dry rendering plants.