RENDERING SYSTEM
Fishmeal Plant
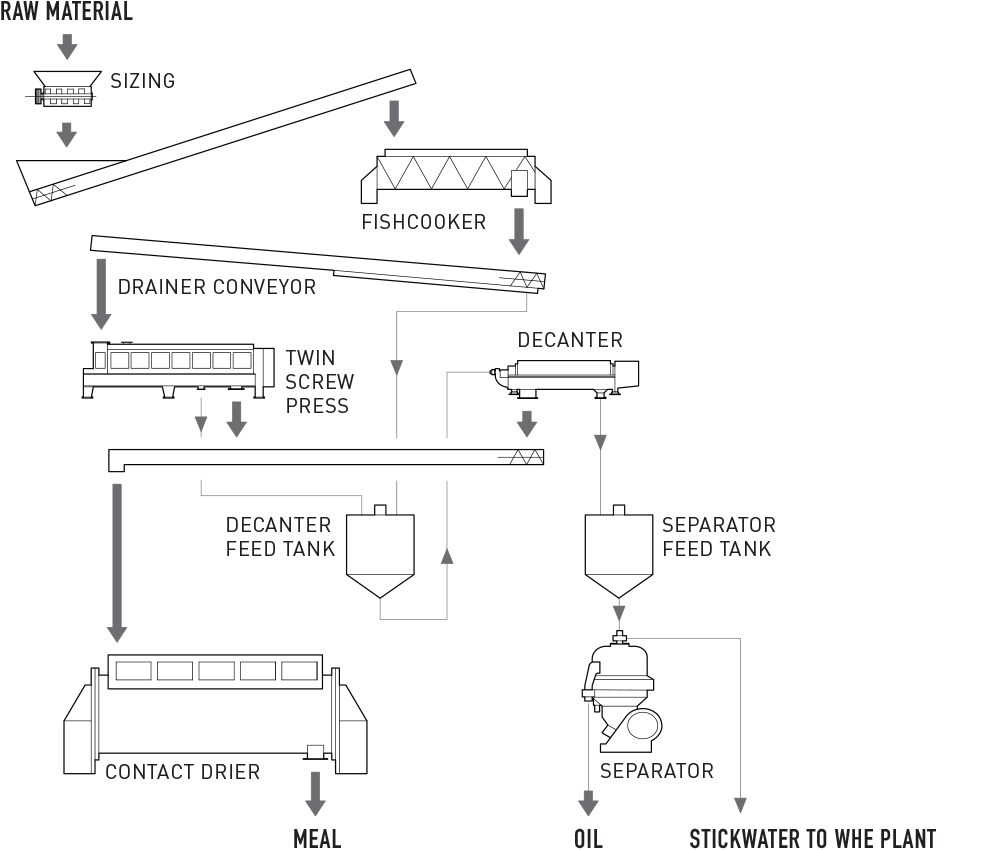
The Rendertech Fishmeal Process (FMP) is a low-temperature wet rendering process suitable for producing fishmeal at raw material capacities of up to 15 tonne/hr and above. It produces better-quality end products with high digestibility, has low energy consumption and is simple to operate. When fitted with a Rendertech Waste Heat Evaporator for stickwater recovery, the process is virtually ‘zero waste’, resulting in high product yield and low wastewater loads.