RENDERING SYSTEM
Centrifuge Dewatering System
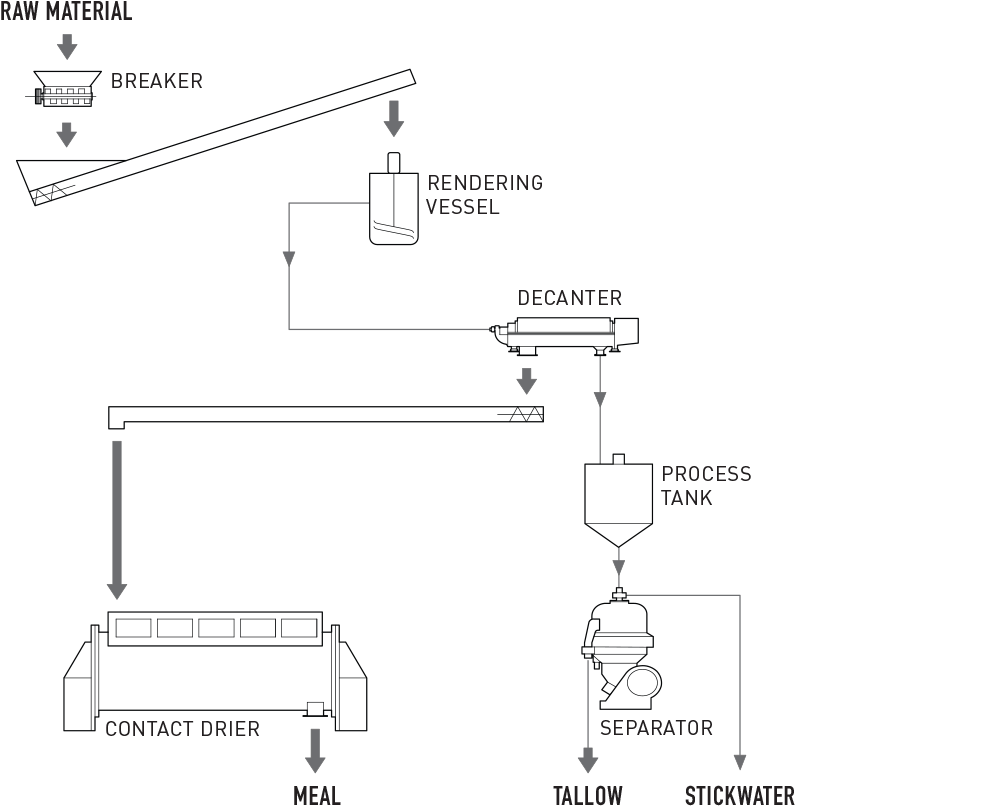
The Rendertech Centrifuge Dewatering System (CDS) is a low-temperature wet rendering process suitable for plant raw material capacities up to 8 tonnes/hr. The system produces quality products, has low energy consumption, and is simple to operate. The compact, versatile plant can process a wide range of raw materials. When fitted with a Rendertech Waste Heat Evaporator for stickwater recovery, the process is virtually ‘zero waste’, resulting in high product yield and low wastewater loads.