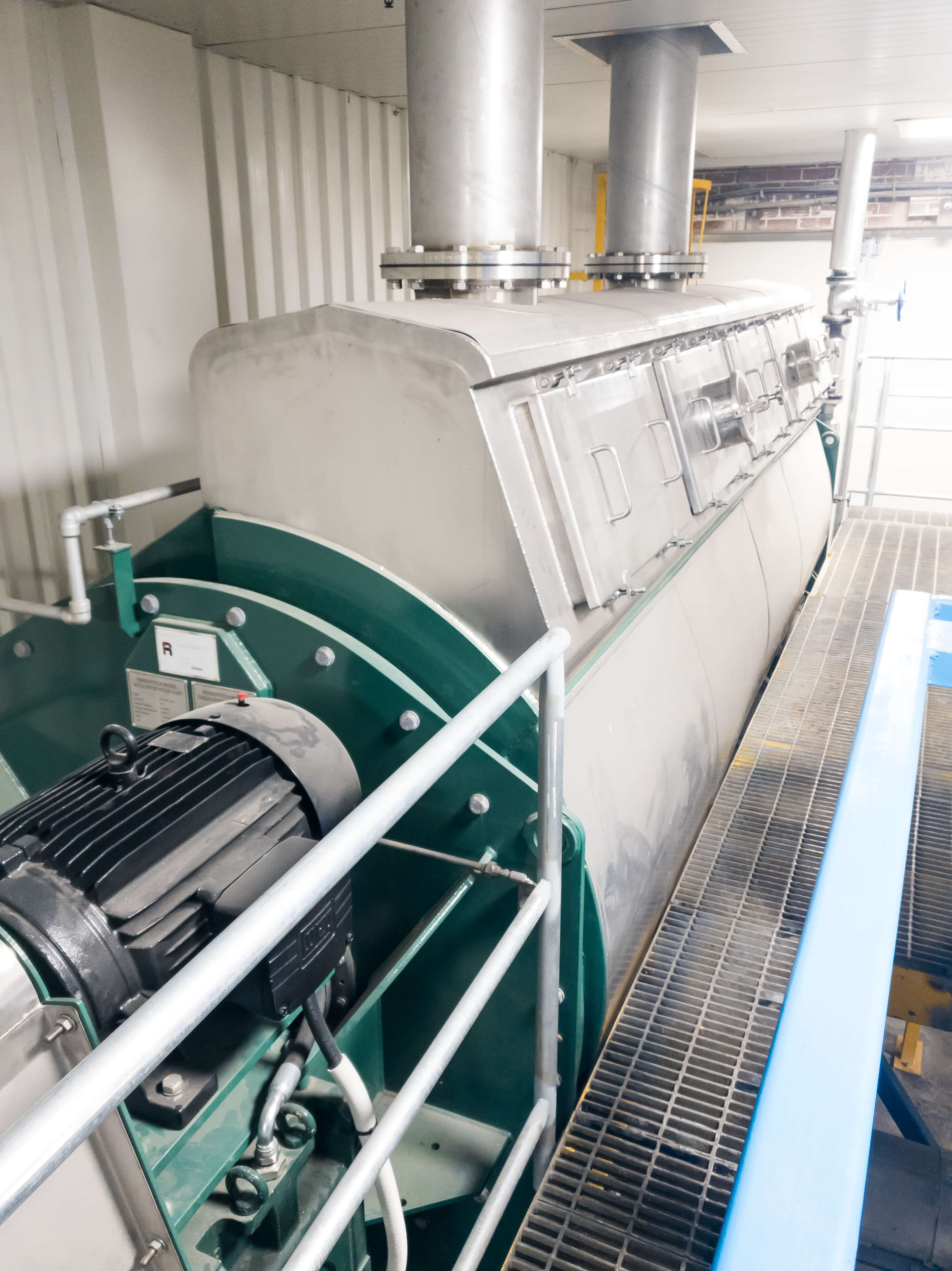
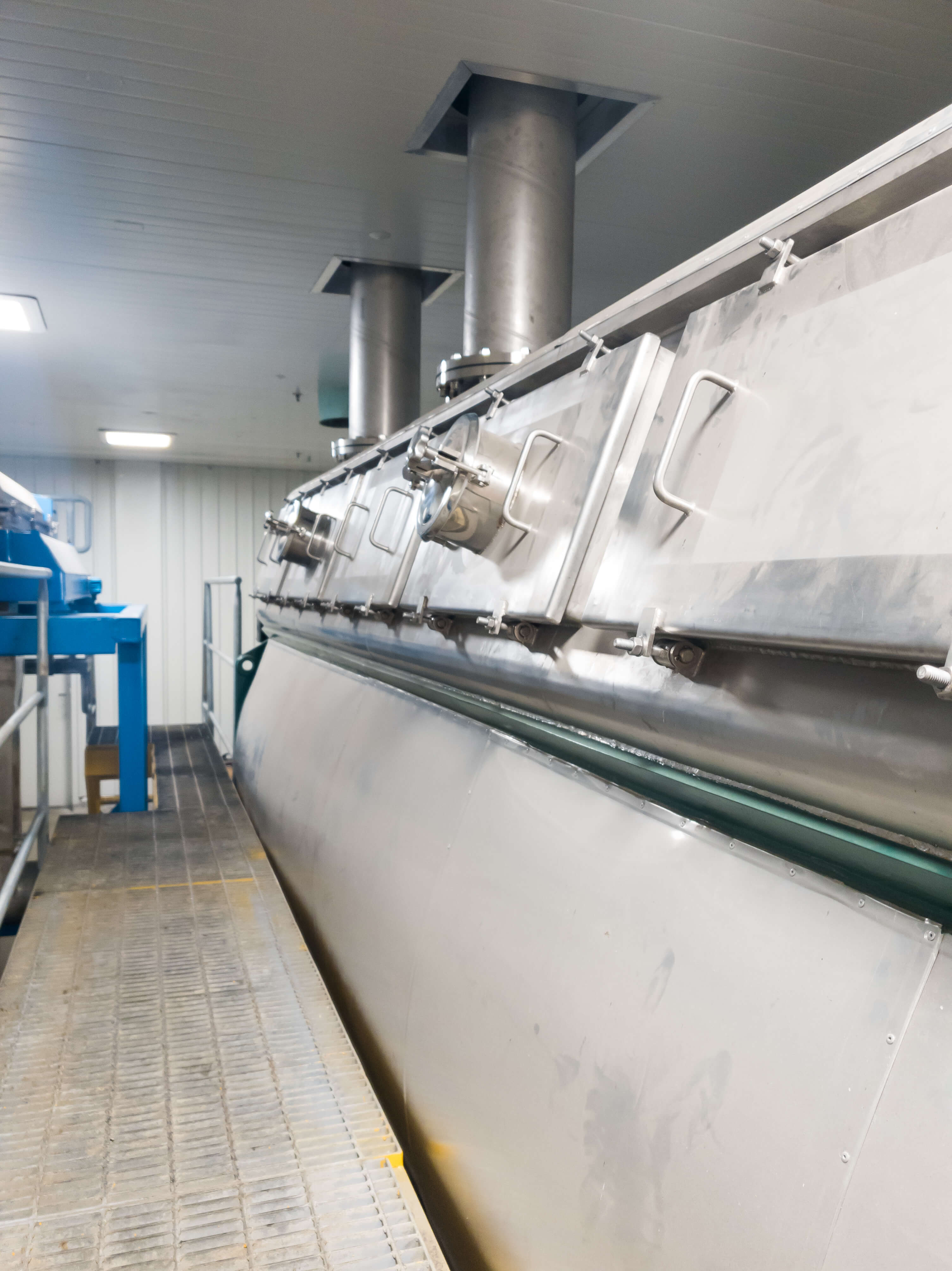
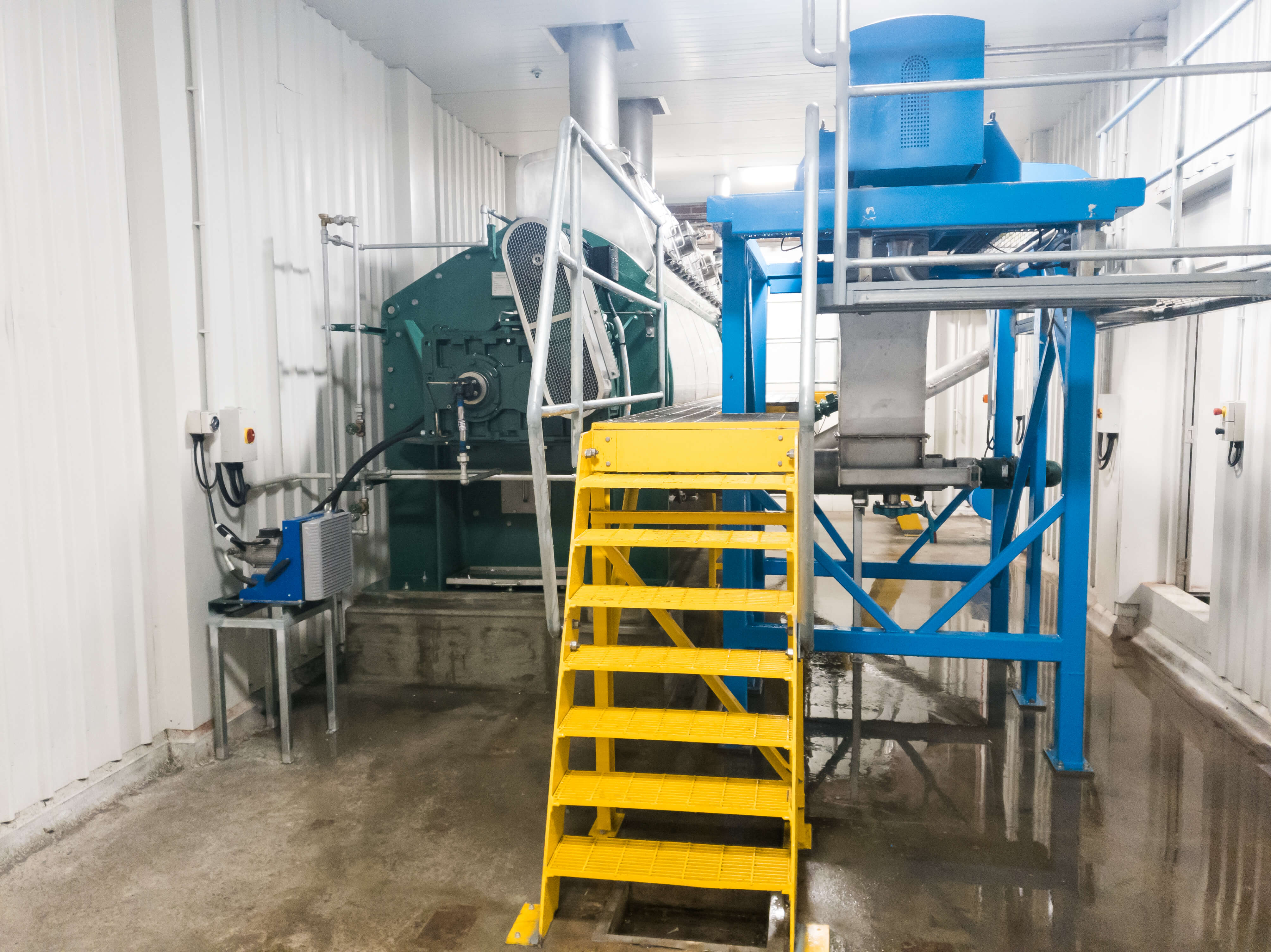
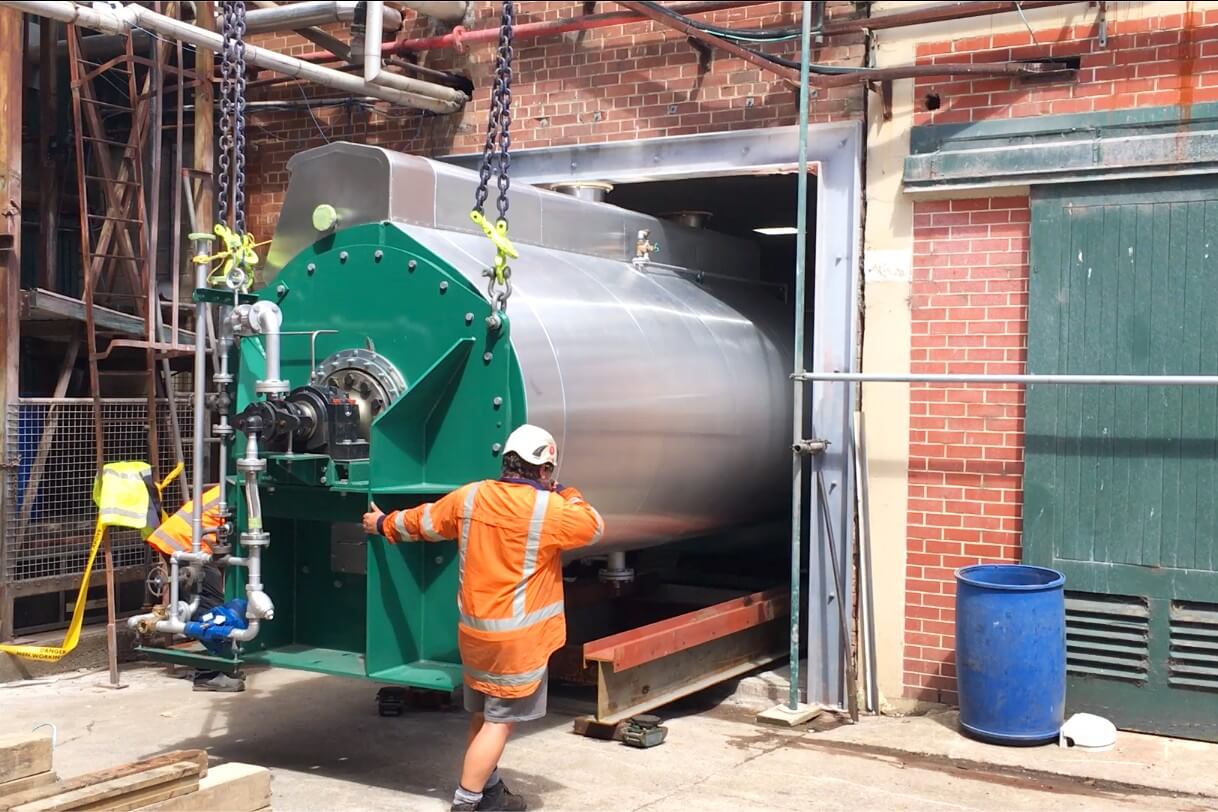
Designing a new rendering plant utilising existing equipment
Prime Range Meats is a privately owned company in Invercargill that processes beef and lamb. Its new owners needed to increase capacity, and commissioned Rendertech to design and install a new rendering plant reusing some of the existing equipment, while combining it with new equipment to meet today’s higher environmental standards and for higher plant throughput.
THE CHALLENGE
Some of the existing equipment had come to the end of its life or did not reflect modern rendering practice, being unreliable and difficult to operate and with out-of-specification end-products.
OUR SOLUTION
With a fixed budget for the upgrade, we designed a new rendering plant reusing as much of the existing equipment as possible, reconfiguring elements so that the system worked correctly.
We also supplied essential new equipment, including a Contact Drier, a Continuous Wool Hydrolyser, new screw conveyors, new pumps and instrumentation. To complete the system, we facilitated the purchase of a refurbished Separator from GTech New Zealand.
We then manufactured the new equipment, detailed the final process design and commissioned the plant.
A proven solution
The solution we provided was the Rendertech Centrifuge Dewatering System (CDS). This system is an energy-efficient, low-temperature process
with a track record of 40 years. It utilises a Grinder and a Rendering Vessel followed by a Centrifuge Decanter for solids/liquid
separation. It is well suited to plants with smaller throughputs and requires lower capital cost than some other systems.
We provided installation drawings so that Prime Range Meat engineers could undertake the installation themselves. We supplemented this by installing the Contact Drier onto the plinths. Lastly, we commissioned the plant and trained the plant operators in the use of the new system.
The result is that Prime Range Meats now have a reliable process which keeps up with their abattoir production, meaning they need not send valuable co-products offsite for rendering by a third party.
Equipment used
Contact Drier, Continuous Wool Hydrolyser, Screw Conveyors, pumps and instrumentation.